What to Expect:
In this episode, Claire Dancer delves into her groundbreaking research on ceramics. Claire shares her journey from studying materials science in the UK to leading research at the University of Warwick. She discusses her work on re-engineering ancient ceramic recipes to create advanced materials with new properties.
About the Guest:
Claire Dancer
Claire Dancer is a researcher at the University of Warwick specializing in ceramics and materials science. Her work focuses on understanding and innovating ancient ceramic recipes to create advanced materials with new properties.
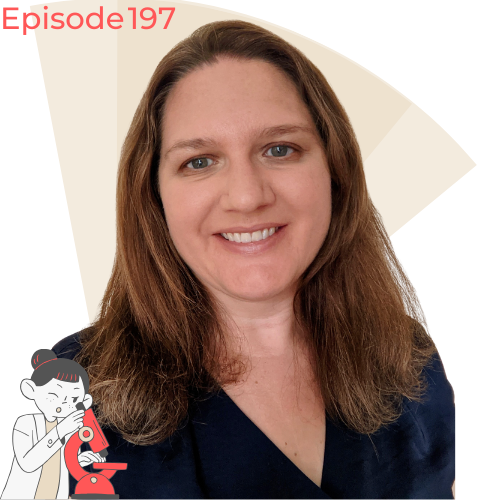
🌟 Key Takeaways from This Episode:
- Ceramics Research: Innovating ancient ceramic recipes to create advanced materials.
- Career Journey: From studying materials science in the UK to leading groundbreaking research at Warwick.
- Favorite Experiment: Re-engineering ancient ceramic recipes for modern applications.
🔬 In This Episode, We Cover:
Claire’s Research :
Claire’s research focuses on innovating ancient ceramic recipes. By understanding the composition and methods used in historical ceramics, she aims to create advanced materials with new properties for modern applications.
Claire’s Career Journey :
Claire’s academic journey began with a Bachelor’s in Materials Science in the UK. She pursued her passion for ceramics, leading her to conduct innovative research at the University of Warwick. Her diverse experiences have enriched her research perspectives and expertise.
Claire’s Favourite Research Experiment :
Claire’s favorite experiment involves re-engineering ancient ceramic recipes for modern applications. By studying historical ceramic techniques, she aims to develop new materials with unique properties that can be used in various industries.
Life as a Scientist – Beyond the Lab:
Claire values the collaborative nature of scientific research and enjoys engaging with the global scientific community. She is passionate about teaching and mentoring the next generation of scientists and values the opportunity to work in a cutting-edge field.
Claire’s 3 Wishes
- Increased funding for research: Claire wishes for more financial support to advance innovative research projects.
- Greater collaboration between researchers: She advocates for stronger partnerships to enhance knowledge sharing and collaborative efforts in research.
- Improved public understanding of scientific research: Claire emphasizes the importance of public awareness and support for scientific advancements.
Claire’s Time on @RealSci_Nano:
Claire will be taking over the RealSci_Nano Twitter account to share her research on ceramics. Followers can expect to learn about the innovative techniques and materials her work focuses on, as well as insights into the future of materials science.
Join the Conversation
Follow & listen to “Under the Microscope” on Spotify, Apple Podcasts, Castbox, Amazon Music, Goodpods.
Got your own favourite podcast app? Follow the RSS link to find Under the Microscope.
Watch the video of all Under the Microscope episodes on The Science Talk’s YouTube channel. While you are at it, make sure to subscribe to our YouTube Channel.
Learn more about Under the Microscope – https://thesciencetalk.com/under-the-microscope/
Love what we do? Support us:
We also offer partnerships to scientists, research institutions, industry, funding bodies & societies.
Get in touch to start the conversation.